Single Pass Powder Induction
The JOBY-NATOR Single Pass Powder Induction System is designed for hydrating and dissolving powders without any recirculation.
The POWDER INDUCTION SYSTEMS of today work in one of a few ways. Either a liquid ring pump (or a twin screw pump) sucks powder into a liquid stream and pushes it through an inline mixer to disperse the powder. OR a pump is used to maintain pressure and velocity across an eductor which creates a Venturi effect and sucks the powder into a liquid stream and (sometimes) then goes through an inline mixer. Both of these methods are very effective on pulling powder into a liquid stream of relatively low viscosity liquid in a recirculated batch process. However, these methods do fall short in several areas:
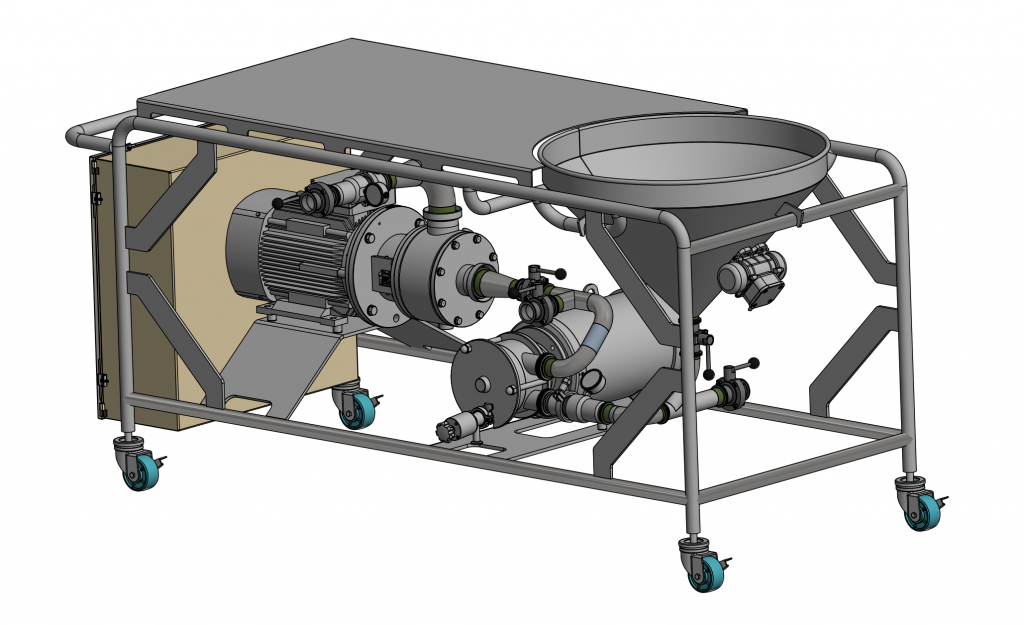
- There is virtually no control over the POWDER to LIQUID ratio so these systems must be used in a recirculated batch process and are not viable as a single pass solution.
- Because vacuum is used to “suck” powder into the liquid stream, the resulting mixture is unnecessarily aerated.
- As the base liquid gets thicker, the ability to suck the powder into the liquid stream decreases drastically. Even using a PD pump to suck the powder is very limited by the liquid viscosity.
Let’s face it, the whole purpose of these powder induction systems is to sell INLINE MIXERS. The focus was on the mixer — not the actual powder incorporation. We are happy to share this with anyone who wants to make their systems better. We can retrofit to virtually any system.
The JOBY-NATOR method does not use vacuum to SUCK powders into the liquid stream. It uses gravity! The powder can either be metered inferentially with an auger at a fixed speed or gravimetrically using load cells. Both methods are far more repeatable and more accurate than using hand or actuated valves to control powder flow.
The powder is metered through the “powder horn” which discharges into the center of the liquid feed. The liquid feed is metered to the outer tube by way of a flowmeter and/or control valve. This makes the POWDER to LIQUID ratio highly accurate and highly repeatable in a single pass.
Traditional powder inductions systems try to suck as much powder into the liquid as they can early in the process while the liquid is at a low viscosity. This means that once all of the powders are inducted into the batch, the entire contents of the batch must be recirculated for an extended period of time. Once the batch is turned over a minimum of 3 times, the batch is deemed homogenous. With a single pass system, no recirculation is required!
By eliminating the recirculation time, the processing time to make the batch is cut to a fraction while also reducing the horsepower requirements of the pumps and mixers. This can also reduce the piping size required since the flow rates are so much lower.
PAYBACK EXAMPLE:
1000-GALLON BATCH PROCESS WITH 25% SOLIDS
TRADITIONAL METHOD
- Begin by filling the batch tank with 7,500 lbs (900 gallons) of water (~10 minutes)
- Suck 2500 lbs. of powder into the liquid in 10 minutes (250 lbs/min)
- Recirculate at 100 GPM for ~31 minutes for homogeniety
- REQUIREMENTS
- 3” lines
- 20HP Pumps & Mixer
- 120 GPM required for CIP
- Time required to clean the tank
TOTAL BATCH TIME: ~40 – 50 minutes
THE JOBY-NATOR METHOD
- Meter water and powder to the JOBY-NATOR at a rate of 50 GPM of water while metering 125 lbs/min of powder (20 minutes)
- REQUIREMENTS
- 2” lines
- 10HP Pumps & Mixer
- 50 GPM required for CIP
- No time, water or chemicals required to clean a batch tank
- On-demand supply to other batching areas / smaller footprint
TOTAL BATCH TIME: ~20 MINUTES
The payback on the added cost of a JOBY-NATOR system equals the cost of the extra time required to recirculate plus any energy savings from being able to use less horsepower.
The metering equipment required for single pass solutions is a one time cost adder. However, the labor and energy savings go on in perpetuity.
What is your actual cost of recirculation? How many more batches can you make in a day if you cut out the recirculation time? How much more accurate and consistent will your end products be if the system controls the feed rates instead of a human being?