ALLERGEN ISOLATED DOSING SYSTEMS
The Infini-MixTM Allergen Isolated Dosing Systems are built for today’s food & beverage manufacturers who run a wide variety of products and need to be able to change recipes quickly. Changing over from a finished product that contains an allergen is time consuming, labor intensive and requires thorough cleaning of the entire process. Until now!
-
Nuts -
Egg -
Wheat -
Dairy
Most processing plants try to run the products containing allergens at the end of the day or in areas that are sectioned off from the primary processing areas. What if you are a company that runs 24/7 and there is no “end of the day” and there is no room to spare?
Late Stage Differentiation
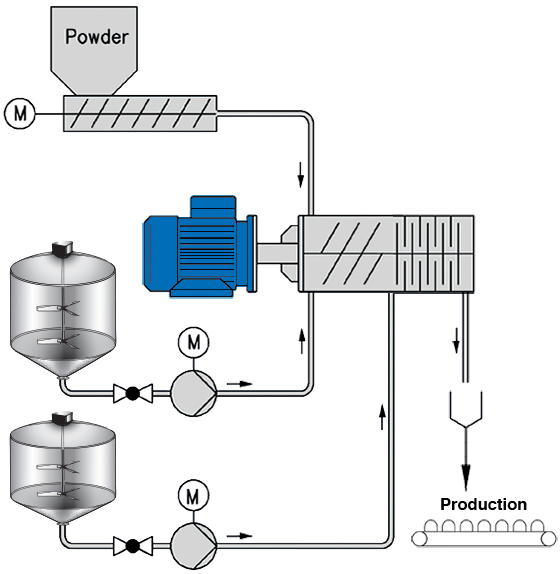
Late Stage Differentiation, or what we call “end of pipe” applications, is where the final ingredient, or set of ingredients, are added to the primary product at the end of the process. This would be like adding fruit to a yogurt or nuts to a chocolate bar or a fragrance to a detergent. These final ingredients can be solids, liquids or gasses. In this case, the final ingredient would be the allergen.
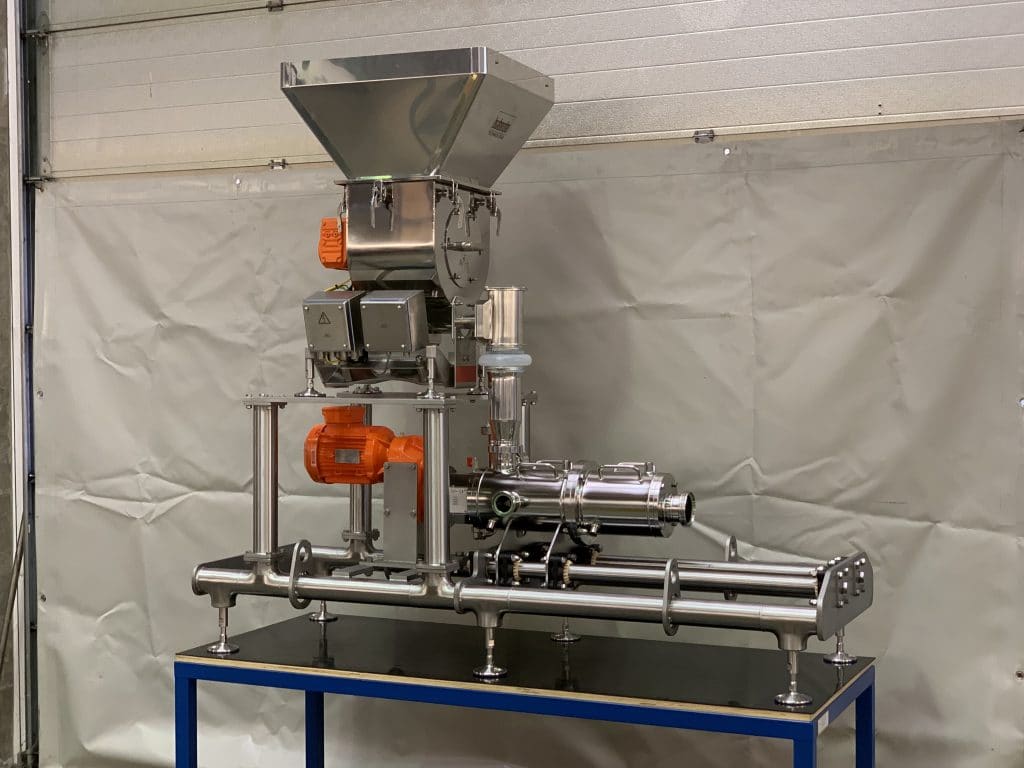
An Infini-MixTM Allergen Isolated Dosing System is a self-contained skid, typically mobile, that can be either be moved in and out of production area in order to dose an allergen into a specific product, or dose from an isolated area. When the run is finished, the dosing system is able to clean itself in place with only a connection to the CIP supply.
EXAMPLE
A bakery that makes cakes has a few batters that require nuts. Their entire process is a batch process and all ingredients are blended into the batch. When the product with the allergen has finished transferring to the depositor, the entire process must be cleaned. The batch tanks, all piping, valving, pumps and instruments must go through a CIP.
Instead, when it is time to run the allergen, they wheel the Allergen Isolated Dosing skid to the packaging area. The skid is fed with the primary batter from the batch tank while the system accurately doses the nuts directly into the batter stream and gently mixes. The blended product gravity feeds directly into the depositor.
When the run is complete, the batter feed line from the batch tanks is disconnected and a jumper to the CIP supply is connected. The twin screw pump on the skid generates the velocity to clean the skid. Meanwhile, the batter feed line can be flushed to get ready for the next product.
Allergen Isolated Dosing Systems can be designed with a wide range of safeguards including dust collection, “auto-allergen supply” to the dosing system and localized standalone CIP capability.